Fasteners and Machining: Customized Solutions for Every Production Demand
Wiki Article
Navigating the World of Fasteners and Machining: Strategies for Accuracy and Rate
In the detailed realm of fasteners and machining, the quest for precision and rate is a continuous obstacle that demands careful focus to information and critical planning. From comprehending the diverse selection of fastener kinds to choosing optimum products that can withstand strenuous needs, each action in the process plays a critical duty in achieving the wanted result.Understanding Bolt Types
When picking fasteners for a project, understanding the various kinds readily available is critical for ensuring ideal performance and integrity. Fasteners come in a vast array of kinds, each developed for particular applications and demands. Bolts are used with nuts to hold products with each other, while screws are functional bolts that can be used with or without a nut, depending upon the application. Nuts, on the other hand, are inside threaded bolts that companion with bolts or screws, providing a safe hold. Washers are essential for distributing the lots of the fastener and stopping damages to the product being fastened. Additionally, rivets are long-term bolts that are optimal for applications where disassembly is not called for. Understanding the differences in between these bolt types is important for picking the right one for the work, making certain that the connection is strong, durable, and reputable. By selecting the appropriate fastener type, you can maximize the efficiency and long life of your job - Fasteners and Machining.
Selecting the Right Products
Comprehending the significance of choosing the best products is vital in ensuring the optimum performance and integrity of the picked fastener kinds reviewed previously. When it concerns bolts and machining applications, the material option plays an important function in determining the general strength, longevity, rust resistance, and compatibility with the desired setting. Different products offer varying residential properties that can dramatically impact the performance of the bolts.Typical materials used for bolts consist of steel, stainless steel, titanium, light weight aluminum, and brass, each having its unique staminas and weaknesses. Steel is renowned for its high strength and toughness, making it appropriate for a broad variety of applications. Choosing the ideal material entails considering factors such as toughness requirements, environmental problems, and spending plan restrictions to ensure the desired efficiency and long life of the fasteners.
Precision Machining Techniques

Along with CNC machining, other accuracy techniques like grinding, turning, milling, and boring play important roles in fastener manufacturing. Grinding helps accomplish great surface area finishes and limited dimensional tolerances, while transforming is frequently made use of to create cylindrical components with precise sizes. Milling and boring operations are essential for forming and creating openings in bolts, guaranteeing they meet precise specifications and feature correctly.
Enhancing Speed and Efficiency
To optimize fastener manufacturing processes, it is essential to enhance operations and implement reliable techniques that enhance precision machining methods. Automated systems can manage repeated tasks with precision and rate, permitting employees to concentrate on more complex and value-added activities. By integrating these approaches, suppliers can achieve an equilibrium in between speed and accuracy, inevitably boosting their competitive edge in the fastener industry.Quality Assurance Steps
Executing extensive quality control procedures is critical in ensuring the integrity and consistency of fastener products in the production process. Fasteners and Machining. Quality control steps encompass various stages, beginning from the option of raw products to the last inspection of the completed bolts. This involves assessing aspects such as product toughness, toughness, and structure to assure that the fasteners fulfill industry standards.Normal calibration of tools and machinery is essential to preserve consistency in manufacturing and ensure that bolts satisfy the needed resistances. Applying rigorous procedures for determining and resolving defects or non-conformities is important in preventing substandard items from getting in the market. By establishing an extensive quality assurance framework, suppliers can copyright the credibility of their brand name and deliver bolts that meet the greatest criteria of performance and longevity.
Conclusion
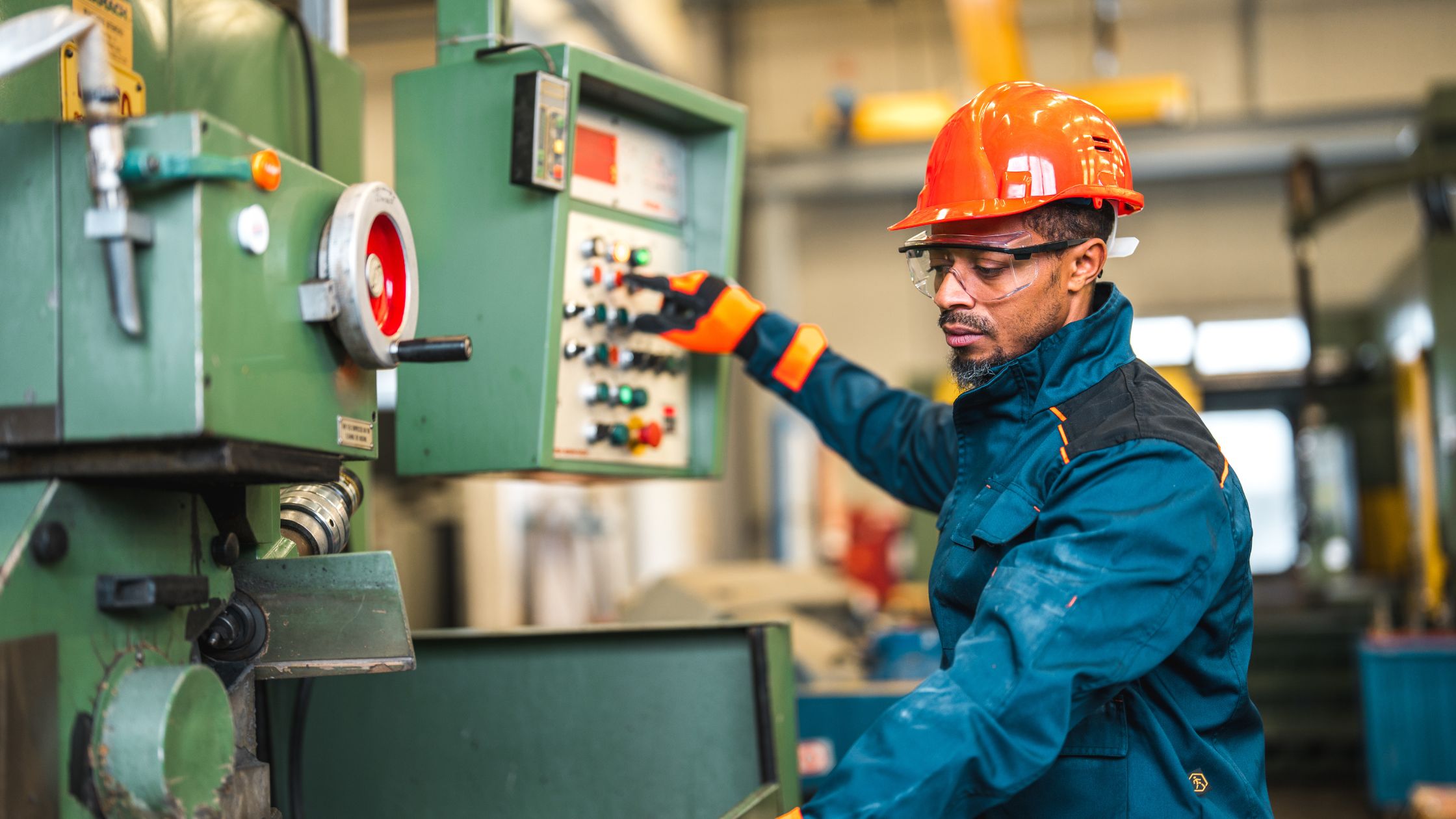
In the elaborate world of fasteners and machining, the mission for precision and rate is a perpetual challenge that requires careful attention to detail and critical preparation. When it comes to fasteners and machining applications, the product option plays an essential role in determining the overall stamina, longevity, corrosion resistance, and compatibility with the intended setting. Precision machining includes various sophisticated methods that make sure the tight resistances and requirements required for bolts.In addition to CNC machining, other accuracy techniques like grinding, turning, visit this website milling, and drilling play essential roles in bolt manufacturing.To enhance bolt manufacturing processes, it is vital to enhance operations and more info here apply efficient strategies that match accuracy machining methods.
Report this wiki page